In the rapidly evolving automotive industry, electronics play a pivotal role in driving innovation, enhancing vehicle performance, and ensuring safety.
Modern vehicles are equipped with a myriad of electronic systems, including Engine Control Units (ECUs), infotainment systems, Advanced Driver Assistance Systems (ADAS), and Electric Power Steering (EPS), all of which contribute to a seamless driving experience and improve safety features.
Test and measurement are crucial in this context, serving as the backbone for validating the functionality, performance, and reliability of these complex systems.
As automotive electronics become increasingly sophisticated, the need for robust testing methodologies and precise measurement techniques has never been more critical.
Ensuring that these systems perform optimally under various conditions and adhere to stringent safety standards is essential for maintaining vehicle safety and enhancing user satisfaction.
This blog explores the challenges, methods, tools, and best practices associated with testing and measurement in automotive electronics.
It highlights how these practices are vital for achieving the high standards required in today’s advanced vehicles, ensuring both performance and safety for drivers and passengers alike.
Key Automotive Electronic Systems
Modern vehicles are technological marvels, packed with sophisticated electronic systems that enhance performance, safety, and the overall driving experience.
These key automotive electronic systems play a vital role in the functionality and reliability of contemporary automobiles. Below are some of the most critical systems:
1. Engine Control Units (ECUs)
The Engine Control Unit (ECU) is the brain of the vehicle’s engine management system.
It controls various engine functions, including fuel injection, ignition timing, and emission controls.
By constantly monitoring the engine’s performance, the ECU ensures optimal efficiency, power output, and compliance with environmental regulations.
Testing the ECU is crucial to guarantee it operates correctly under all driving conditions and effectively manages the engine’s performance.
2. Infotainment Systems
Infotainment systems combine entertainment and information delivery within the vehicle.
These systems provide navigation, audio and video playback, internet connectivity, and smartphone integration.
They are designed to enhance the driving experience by offering convenience and entertainment while minimizing distractions.
Testing infotainment systems involves validating user interfaces, connectivity features, audio and video quality, and system integration with other vehicle electronics.
3. Advanced Driver Assistance Systems (ADAS)
ADAS technologies are designed to improve vehicle safety and driver comfort.
Key features include adaptive cruise control, lane departure warning, automatic emergency braking, and parking assistance.
These systems rely on sensors, cameras, radar, and lidar to monitor the vehicle’s surroundings and assist the driver in making safe decisions.
Testing ADAS is critical to ensure accurate detection, timely responses, and seamless integration with the vehicle’s control systems.
4. Electric Power Steering (EPS)
Electric Power Steering (EPS) replaces traditional hydraulic steering systems with electric motors, providing more precise control and reducing engine load, which enhances fuel efficiency.
EPS systems adjust the steering based on vehicle speed and driving conditions, improving maneuverability and stability.
Testing EPS involves assessing the system’s responsiveness, reliability, and integration with other vehicle safety features.
5. Battery Management Systems (BMS)
In electric and hybrid vehicles, the Battery Management System (BMS) is essential for monitoring and managing the vehicle’s battery pack.
It ensures the battery operates within safe parameters, optimizes charging and discharging cycles, and extends the battery’s lifespan.
Testing BMS is vital to confirm accurate monitoring, effective thermal management, and reliable communication with the vehicle’s control systems.
6. Body Control Modules (BCM)
Body Control Modules (BCM) manage various electronic accessories and features within the vehicle, such as lighting, climate control, power windows, and door locks.
These modules ensure the proper functioning of non-engine-related systems and enhance the vehicle’s comfort and convenience.
Testing BCM involves verifying the functionality, user interface, and integration of these electronic accessories.
In summary, these key automotive electronic systems are integral to modern vehicle performance, safety, and driver experience.
Rigorous testing and precise measurement are essential to ensure these systems function correctly, interact seamlessly, and meet the high standards expected in today’s automotive industry.
Testing Challenges in Automotive Electronics
As automotive electronics become increasingly complex, testing these systems presents a unique set of challenges.
Ensuring the reliability, safety, and performance of electronic components in modern vehicles requires overcoming several hurdles.
Below are some of the primary testing challenges faced in automotive electronics:
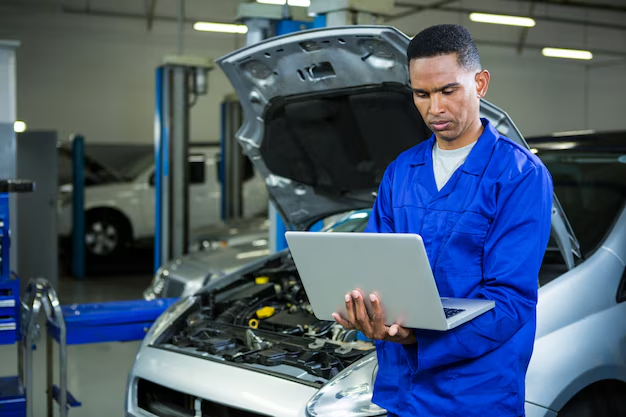
1. Complexity of Modern Automotive Electronics
Modern vehicles are equipped with a multitude of interconnected electronic systems, each with its own set of functions and requirements.
The integration of these systems, such as Engine Control Units (ECUs), Advanced Driver Assistance Systems (ADAS), infotainment systems, and Electric Power Steering (EPS), creates a complex network that must be thoroughly tested.
Ensuring seamless communication and interoperability among these systems is a significant challenge, necessitating comprehensive testing methodologies.
2. Diverse Operating Conditions and Environments
Automotive electronics must operate reliably under a wide range of environmental conditions, including extreme temperatures, humidity, vibration, and electromagnetic interference.
Testing these systems requires simulating these harsh conditions to ensure they can withstand real-world scenarios.
This involves environmental testing chambers, vibration testing rigs, and electromagnetic compatibility (EMC) testing to validate performance under various stresses.
3. Integration with Other Vehicle Systems
Automotive electronics do not function in isolation; they must integrate seamlessly with mechanical components, software, and other electronic systems within the vehicle.
Testing must account for this integration to ensure that electronic systems work harmoniously with the vehicle’s overall architecture.
This requires end-to-end testing approaches that consider the interactions between different systems and subsystems.
4. Safety and Compliance Requirements
Automotive electronics are subject to stringent safety standards and regulatory requirements, such as ISO 26262 for functional safety.
Meeting these standards involves rigorous testing to identify and mitigate potential safety risks.
Ensuring compliance with regulatory requirements adds another layer of complexity to the testing process, requiring detailed documentation and validation of safety features.
5. Rapid Technological Advancements
The automotive industry is constantly evolving, with new technologies such as autonomous driving, electric vehicles, and connected car features emerging at a rapid pace.
Keeping up with these advancements and ensuring that testing methodologies evolve accordingly is a significant challenge.
Test engineers must continuously update their knowledge and skills to effectively test new technologies and ensure their reliability and safety.
6. Software Complexity and Updates
As vehicles become more software-driven, the complexity of automotive software increases.
This includes the software running on ECUs, infotainment systems, and ADAS.
Testing this software involves not only functional and performance testing but also ensuring that over-the-air (OTA) updates do not introduce new issues.
Validating software updates and patches is crucial to maintaining system integrity and performance.
7. Cybersecurity Threats
With the rise of connected and autonomous vehicles, cybersecurity has become a critical concern in automotive electronics.
Testing must include rigorous security assessments to identify and mitigate vulnerabilities that could be exploited by cyberattacks.
Ensuring the security of vehicle electronics requires specialized testing techniques and continuous monitoring to protect against emerging threats.
8. Cost and Time Constraints
Comprehensive testing of automotive electronics is both time-consuming and costly.
Manufacturers must balance the need for thorough testing with the pressures of reducing time-to-market and controlling costs.
This often involves prioritizing critical tests and leveraging advanced testing tools and automation to improve efficiency without compromising quality.
Testing Methods and Techniques
To ensure the performance, reliability, and safety of automotive electronics, a variety of testing methods and techniques are employed.
These methods are designed to validate different aspects of electronic systems, from functional operations to long-term durability.
Below are some of the key testing methods and techniques used in the automotive industry:
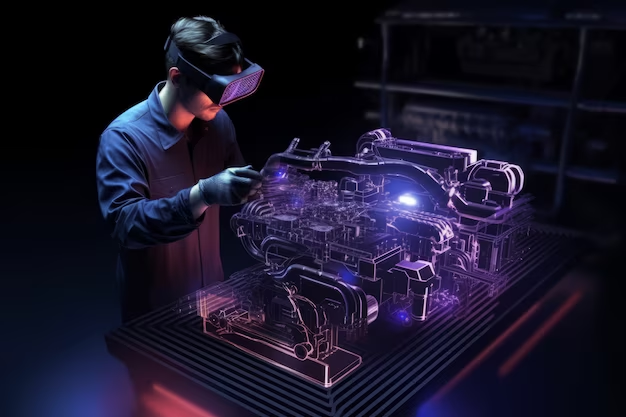
1. Functional Testing
Functional testing involves verifying that each electronic system performs its intended functions correctly.
This type of testing checks the inputs and outputs of the system to ensure they meet specified requirements.
Functional testing can be conducted at different stages of development, from individual components to fully integrated systems. Key aspects include:
- Unit Testing: Testing individual components or units to ensure they function correctly in isolation.
- Integration Testing: Verifying that different components or subsystems work together as expected.
- System Testing: Assessing the complete system to ensure all integrated parts function as intended.
2. Performance Testing
Performance testing evaluates how well electronic systems perform under various conditions.
This includes assessing responsiveness, efficiency, and reliability. Key performance metrics such as processing speed, data throughput, and latency are measured to ensure the system meets performance expectations. Performance testing techniques include:
- Load Testing: Assessing system behavior under normal and peak load conditions.
- Stress Testing: Evaluating system performance under extreme conditions to identify potential failure points.
- Scalability Testing: Determining how well the system can handle increased load by adding resources.
3. Durability Testing
Durability testing, also known as reliability testing, evaluates how electronic systems perform over time under different conditions.
This type of testing simulates long-term usage to identify potential wear and tear or failure points. Techniques used in durability testing include:
- Accelerated Life Testing: Simulating extended periods of usage in a shorter time frame to predict long-term reliability.
- Thermal Cycling Testing: Subjecting systems to repeated temperature changes to assess thermal stress resilience.
- Vibration Testing: Exposing systems to mechanical vibrations to evaluate structural integrity and performance under physical stress.
4. Safety Testing
Safety testing ensures that automotive electronics comply with safety standards and regulations.
This type of testing identifies and mitigates potential safety risks, ensuring that systems operate safely under all conditions. Key safety testing techniques include:
- Fault Injection Testing: Deliberately introducing faults to assess system behavior and fault tolerance.
- Hazard Analysis and Risk Assessment (HARA): Identifying potential hazards and evaluating their risks to ensure compliance with safety standards like ISO 26262.
- Fail-Safe Testing: Verifying that systems enter a safe state in the event of a failure.
5. Environmental Testing
Environmental testing assesses how electronic systems perform under various environmental conditions.
This includes exposure to extreme temperatures, humidity, dust, and electromagnetic interference. Key environmental testing techniques include:
- Thermal Testing: Evaluating system performance under high and low-temperature conditions.
- Humidity Testing: Assessing system resilience to moisture and humidity.
- Electromagnetic Compatibility (EMC) Testing: Ensuring systems can operate without interference from or causing interference to other electronic devices.
6. Software Testing
Software testing is crucial for validating the functionality, performance, and security of the software running on automotive electronic systems. This includes:
- Static Code Analysis: Reviewing code for potential errors or vulnerabilities without executing it.
- Dynamic Testing: Running the software to identify bugs, performance issues, and security vulnerabilities.
- Regression Testing: Ensuring new code changes do not adversely affect existing functionality.
7. Automated Testing
Automated testing leverages tools and scripts to perform repetitive and complex testing tasks efficiently.
This approach is particularly useful for large-scale testing and regression testing. Benefits of automated testing include increased test coverage, faster execution, and reduced human error.
8. Hardware-in-the-Loop (HIL) Testing
HIL testing involves integrating real hardware components with simulated systems to validate performance in a controlled environment.
This technique allows for comprehensive testing of electronic control units (ECUs) and other critical systems without requiring a fully assembled vehicle.
Tools and Equipment for Automotive Testing
Ensuring the reliability, safety, and performance of automotive electronics requires specialized tools and equipment.
These instruments are designed to test and measure various aspects of electronic systems, providing detailed insights into their functionality and performance.
Below are some of the key tools and equipment used in automotive testing:
1. Oscilloscopes and Signal Analyzers
Oscilloscopes and signal analyzers are essential for examining electrical signals within automotive systems.
They allow engineers to visualize waveforms, measure signal characteristics, and diagnose issues related to voltage, timing, and frequency.
- Oscilloscopes: Used to capture and display electrical signals in real-time, helping to identify anomalies and measure signal integrity.
- Signal Analyzers: Measure and analyze the frequency spectrum of electrical signals, crucial for diagnosing issues related to electromagnetic interference (EMI) and signal distortion.
2. Automotive Diagnostic Tools
Automotive diagnostic tools are used to interface with a vehicle’s onboard computer systems, retrieving diagnostic trouble codes (DTCs) and real-time data.
These tools are critical for identifying and troubleshooting issues within the vehicle’s electronic systems.
- OBD-II Scanners: Connect to the vehicle’s onboard diagnostics (OBD) port to read DTCs, monitor system performance, and reset warning lights.
- Diagnostic Software: Provides comprehensive data analysis and reporting, allowing engineers to interpret diagnostic information and develop solutions.
3. Environmental Chambers
Environmental chambers simulate various environmental conditions to test the resilience and performance of automotive electronics.
These chambers can replicate extreme temperatures, humidity levels, and other environmental factors to ensure systems can withstand real-world conditions.
- Temperature Chambers: Subject electronics to high and low temperatures to test thermal performance and stress.
- Humidity Chambers: Expose systems to varying humidity levels to assess moisture resistance and performance under humid conditions.
4. Vibration Testing Equipment
Vibration testing equipment is used to evaluate the structural integrity and performance of automotive electronics under mechanical stress.
This testing ensures that systems can withstand vibrations caused by road conditions, engine operations, and other sources.
- Shakers: Generate controlled vibrations to simulate real-world mechanical stress and assess system durability.
- Vibration Tables: Provide a platform for testing components and assemblies under various vibration profiles.
5. Electromagnetic Compatibility (EMC) Test Equipment
EMC test equipment measures the electromagnetic emissions from automotive electronics and assesses their susceptibility to external electromagnetic interference.
Ensuring EMC compliance is critical to prevent interference with other electronic systems and to meet regulatory standards.
- EMI Receivers: Measure electromagnetic emissions from electronic systems to ensure they are within acceptable limits.
- Anechoic Chambers: Shielded environments that isolate devices from external electromagnetic signals, allowing for precise EMC testing.
6. Data Loggers and Analyzers
Data loggers and analyzers are used to record and analyze real-time data from automotive systems during testing.
They provide valuable insights into system performance and help identify issues that may not be apparent during static testing.
- Data Loggers: Capture and store data from various sensors and electronic systems for later analysis.
- Real-Time Analyzers: Provide immediate feedback on system performance, allowing engineers to make real-time adjustments and improvements.
7. Hardware-in-the-Loop (HIL) Simulators
HIL simulators integrate real hardware components with simulated systems, allowing for comprehensive testing of electronic control units (ECUs) and other critical systems in a controlled environment.
This technique enables thorough validation of system functionality and interactions without requiring a fully assembled vehicle.
- HIL Test Benches: Provide a platform for integrating hardware and simulation models, enabling detailed testing of ECUs and other systems.
- Simulation Software: Models the behavior of vehicle systems and environments, facilitating realistic testing scenarios.
8. Automated Test Equipment (ATE)
ATE systems automate the testing process, increasing efficiency and consistency.
These systems are particularly useful for large-scale testing and repetitive tasks, reducing the potential for human error and speeding up the testing cycle.
- Test Rigs: Automated setups that perform specific tests on electronic components and systems.
- Automated Test Scripts: Software scripts that control the testing process, execute test cases and generate reports.
9. Network Analyzers
Network analyzers are used to test and validate the performance of automotive communication networks, such as CAN, LIN, and Ethernet.
They ensure reliable data transmission and diagnose issues related to network performance.
- CAN Analyzers: Test and troubleshoot Controller Area Network (CAN) communications.
- Ethernet Analyzers: Validate high-speed data communication over automotive Ethernet networks.
Conclusion
Testing and measurement play a pivotal role in ensuring the performance, reliability, and safety of automotive electronics.
As vehicles become more technologically advanced, the complexity of their electronic systems increases, necessitating robust testing methodologies and specialized tools.
From functional and performance testing to environmental and durability assessments, each testing method addresses specific challenges inherent to automotive electronics.
The use of advanced tools and equipment, such as oscilloscopes, environmental chambers, HIL simulators, and EMC test systems, enables engineers to conduct comprehensive evaluations.
These tools help identify potential issues early in the development process, allowing for timely corrections and improvements.
Automated test equipment and diagnostic tools further streamline the testing process, enhancing efficiency and accuracy.
Ultimately, the rigorous testing of automotive electronics is crucial for delivering safe, reliable, and high-performing vehicles.
By overcoming testing challenges and leveraging cutting-edge tools, the automotive industry can continue to innovate and meet the ever-evolving demands of modern transportation.
As technology advances, so too will the methods and tools used in automotive testing, ensuring that vehicles remain at the forefront of safety and performance.