In today’s competitive market, ensuring product reliability is paramount for maintaining customer satisfaction and brand reputation.
Environmental testing plays a crucial role in this process, simulating extreme conditions to evaluate a product’s durability and performance.
From scorching deserts to freezing arctic environments, products are often exposed to harsh conditions that can impact their functionality and lifespan.
Manufacturers can identify potential weaknesses and make necessary improvements before products reach the market by conducting rigorous environmental tests.
This not only enhances product reliability but also reduces the risk of costly recalls and failures.
In this blog, we will explore the significance of environmental testing, the various types of tests conducted, and how these tests contribute to the overall reliability of products in extreme conditions.
What is Environmental Testing?
Environmental testing refers to a series of assessments designed to determine how products and materials perform under extreme conditions.
These tests simulate a variety of environmental factors such as temperature, humidity, vibration, shock, and corrosion, which products might encounter during their lifecycle.
The goal is to identify any potential weaknesses or failures that could occur when the product is exposed to harsh environments, ensuring it remains reliable and functional.
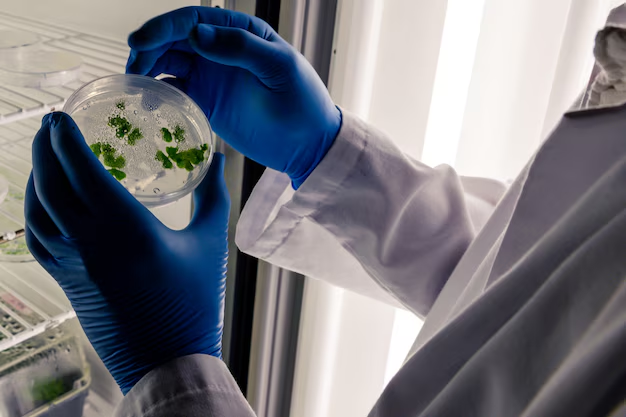
Types of Environmental Tests:
- Temperature Testing:
- High and Low-Temperature Exposure: Products are subjected to extreme heat and cold to assess their performance and durability. This is crucial for items that need to operate in diverse climates.
- Thermal Cycling: This involves repeatedly exposing the product to alternating high and low temperatures to evaluate how well it can handle rapid temperature changes.
- Thermal Shock: A more intense form of thermal cycling, thermal shock testing rapidly transitions the product from one extreme temperature to another to identify potential failures due to thermal stress.
- Humidity Testing:
- High and Low Humidity Exposure: Products are tested in environments with high and low moisture levels to determine their resistance to humidity and potential for corrosion or degradation.
- Humidity Cycling: This test exposes products to fluctuating humidity levels to simulate real-world conditions and assess their long-term durability.
- Vibration Testing:
- Operational Vibration: This test simulates the vibrations a product might experience during normal operation, ensuring that it can withstand these conditions without performance issues.
- Transportation Vibration: Products are also subjected to vibrations they might encounter during shipping and handling to ensure they reach customers in working order.
- Shock Testing:
- Products are exposed to sudden and intense impacts to evaluate their resilience to shock and their ability to maintain functionality after such events.
- Corrosion Testing:
- Salt Spray Testing: This simulates exposure to corrosive environments, such as salty sea air, to assess a product’s resistance to rust and corrosion.
- Humidity and Moisture Testing: Beyond just humidity levels, this testing can also involve prolonged exposure to moist environments to check for long-term durability.
Environmental testing is vital for ensuring that products can survive and function effectively in the real world.
It helps manufacturers identify potential issues early in the development process, leading to improved product quality, reliability, and customer satisfaction.
Why Environmental Testing is Crucial
Environmental testing is a cornerstone of product development and quality assurance, playing a vital role in ensuring that products meet the highest standards of reliability and durability. Here’s why environmental testing is crucial:
- Ensuring Product Reliability:
- Environmental testing helps to guarantee that products can withstand extreme conditions, ensuring they remain reliable and functional throughout their lifecycle. This is particularly important for products used in critical applications, such as aerospace, automotive, and medical devices, where failure can have severe consequences.
- Identifying Potential Failures Early:
- By subjecting products to rigorous environmental tests, manufacturers can identify potential weaknesses and vulnerabilities before the product reaches the market. Early detection of issues allows for timely improvements, reducing the risk of failures in real-world use.
- Compliance with Industry Standards:
- Many industries have stringent regulations and standards that products must meet. Environmental testing ensures compliance with these standards, helping companies avoid legal issues and maintain market access.
- Enhancing Customer Satisfaction:
- Reliable products lead to satisfied customers. By ensuring that products perform well under various environmental conditions, companies can build trust and loyalty among their customer base, enhancing their reputation and brand value.
- Reducing Costs and Risks:
- Identifying and addressing potential issues during the testing phase can significantly reduce the costs associated with product recalls, warranty claims, and repairs. It also minimizes the risk of reputational damage due to product failures.
- Supporting Innovation:
- Environmental testing is essential for the development of innovative products that push the boundaries of technology. By understanding how new materials and designs perform under extreme conditions, companies can innovate with confidence.
- Real-World Simulation:
- Environmental tests simulate the harsh conditions that products may encounter in the real world, such as extreme temperatures, high humidity, vibrations, and shocks. This ensures that products are not only theoretically robust but also practically reliable in their intended environments.
- Enhancing Product Longevity:
- Products that pass environmental testing are more likely to have longer lifespans, providing better value to customers and reducing the environmental impact associated with frequent replacements.
- Gaining Competitive Advantage:
- Companies that invest in thorough environmental testing can differentiate themselves from competitors by offering more reliable and durable products. This can be a significant competitive advantage in markets where quality and performance are key selling points.
- Case Studies of Failures and Successes:
- Real-world examples highlight the importance of environmental testing. For instance, the failure of certain electronics in high humidity conditions due to inadequate testing underscores the need for comprehensive environmental assessments. Conversely, products that succeed in rigorous testing environments often set new benchmarks for industry standards.
Environmental testing is not just a procedural formality; it is a critical step in the product development process that ensures products are safe, reliable, and fit for purpose.
By investing in thorough environmental testing, companies can enhance product quality, meet regulatory requirements, satisfy customers, and maintain a strong competitive edge in the market.
Common Environmental Tests and Their Applications
Environmental testing encompasses a variety of assessments that simulate real-world conditions to evaluate a product’s performance and durability. Here are some of the most common environmental tests and their applications:
- Temperature Testing:
- High and Low-Temperature Exposure: Products are subjected to extreme heat and cold to assess their operational capability and structural integrity. This is essential for electronics, automotive components, and aerospace equipment that must function in diverse climates.
- Thermal Cycling: This involves repeatedly exposing the product to alternating high and low temperatures to evaluate its ability to handle rapid temperature changes. This is critical for materials used in space missions, where temperature variations can be drastic.
- Thermal Shock: Rapidly transitions the product from one extreme temperature to another to identify potential failures due to thermal stress. This test is important for military and defense equipment that may experience sudden environmental changes.
- Humidity Testing:
- High and Low Humidity Exposure: Tests products in environments with varying moisture levels to determine their resistance to humidity and potential for corrosion or degradation. This is vital for consumer electronics, medical devices, and automotive interiors.
- Humidity Cycling: Exposes products to fluctuating humidity levels to simulate real-world conditions and assess their long-term durability. This is particularly relevant for outdoor equipment and infrastructure components.
- Vibration Testing:
- Operational Vibration: Simulates the vibrations a product might experience during normal operation to ensure it can withstand these conditions without performance issues. This is crucial for machinery, vehicles, and industrial equipment.
- Transportation Vibration: Subjects products to the vibrations they might encounter during shipping and handling to ensure they reach customers in working order. This is important for packaged goods, electronics, and delicate instruments.
- Shock Testing:
- Products are exposed to sudden and intense impacts to evaluate their resilience to shock and their ability to maintain functionality after such events. This test is essential for portable devices, military hardware, and automotive crash sensors.
- Corrosion Testing:
- Salt Spray Testing: Simulates exposure to corrosive environments, such as salty sea air, to assess a product’s resistance to rust and corrosion. This is vital for marine equipment, outdoor structures, and automotive parts.
- Humidity and Moisture Testing: Beyond just humidity levels, this testing can involve prolonged exposure to moist environments to check for long-term durability. This is relevant for construction materials, pipelines, and HVAC systems.
- Altitude Testing:
- Simulates high-altitude conditions to evaluate a product’s performance in low-pressure environments. This is crucial for aerospace components, aviation electronics, and high-altitude scientific instruments.
- Electromagnetic Compatibility (EMC) Testing:
- Ensures that electronic products do not emit excessive electromagnetic interference and are immune to external electromagnetic disturbances. This is essential for all electronic devices, especially those used in medical, automotive, and aerospace applications.
- Dust and Water Ingress Testing:
- Ingress Protection (IP) Testing: Determines a product’s resistance to dust and water ingress, ensuring it can operate in harsh environments. This is critical for outdoor electronics, automotive parts, and industrial equipment.
- UV Exposure Testing:
- Simulates prolonged exposure to ultraviolet (UV) light to assess a product’s resistance to UV degradation. This is important for outdoor products, such as solar panels, plastic materials, and coatings.
- Acoustic Testing:
- Measures a product’s noise levels and its ability to withstand and perform under high noise conditions. This is crucial for consumer electronics, automotive components, and industrial machinery.
Each of these tests is designed to mimic real-world conditions and identify potential points of failure, ensuring that products are robust, reliable, and fit for their intended use.
By understanding and applying these tests, manufacturers can enhance product quality and performance, ultimately delivering better value to their customers.
Industry-Specific Applications
Environmental testing is crucial across various industries to ensure that products and systems can withstand the specific challenges they face in their operational environments. Here are some industry-specific applications of environmental testing:
- Aerospace and Defense:
- Equipment Reliability: Aerospace and defense systems, such as aircraft components, satellites, and military hardware, are subjected to extreme temperatures, pressures, and vibrations. Environmental testing ensures these products can endure harsh conditions, from the freezing temperatures of the upper atmosphere to the intense heat of re-entry.
- Safety and Performance: Testing for shock, vibration, and thermal cycling is critical to ensure the safety and performance of critical components used in aircraft and spacecraft, as any failure can have catastrophic consequences.
- Automotive:
- Durability in Various Climates: Automotive components, including engines, electronics, and interior materials, are tested for their ability to perform in diverse climates, from the scorching heat of deserts to the freezing cold of polar regions.
- Vibration and Shock Testing: Ensures that vehicle parts can withstand the vibrations and shocks encountered during driving. This is crucial for the longevity and safety of automotive systems, including suspension components and onboard electronics.
- Electronics:
- Longevity and Performance: Consumer electronics, such as smartphones, laptops, and wearables, undergo environmental testing to ensure they can withstand everyday use, including exposure to humidity, temperature fluctuations, and potential drops or shocks.
- Ingress Protection: Devices are tested for resistance to dust and water ingress, ensuring they can operate in various environments without malfunctioning. This is particularly important for outdoor and portable devices.
- Medical Devices:
- Critical Functionality: Medical devices, including diagnostic equipment, implants, and portable health monitors, must be reliable and safe under various environmental conditions. Testing ensures that these devices function correctly and maintain accuracy in temperature, humidity, and electromagnetic environments.
- Compliance with Regulations: Rigorous testing is required to meet regulatory standards, ensuring patient safety and device efficacy.
- Telecommunications:
- Network Equipment: Telecommunications infrastructure, such as antennas, routers, and switches, is subjected to environmental testing to ensure reliable performance in diverse conditions, from urban environments to remote, harsh locations.
- Durability and Reliability: Testing for temperature extremes, humidity, and electromagnetic interference is essential to maintain uninterrupted communication services.
- Energy and Utilities:
- Renewable Energy Systems: Solar panels, wind turbines, and other renewable energy systems are tested for their ability to withstand environmental stresses such as UV exposure, temperature fluctuations, and corrosion. This ensures their efficiency and longevity.
- Grid Components: Power grid components, including transformers and smart meters, undergo environmental testing to ensure they can operate reliably under various conditions, contributing to overall grid stability.
- Industrial Equipment:
- Operational Efficiency: Industrial machinery and equipment are subjected to environmental testing to ensure they can perform efficiently in harsh operating conditions, such as high temperatures, heavy vibrations, and dusty environments.
- Maintenance and Downtime: Testing helps identify potential failure points, reducing maintenance costs and minimizing downtime in industrial operations.
- Marine:
- Salt Spray and Corrosion Resistance: Marine equipment, including ships, offshore platforms, and underwater vehicles, is tested for resistance to salt spray and corrosion. This ensures the durability and reliability of components exposed to seawater.
- Pressure and Temperature Extremes: Submarine and deep-sea exploration equipment undergoes testing to withstand high pressures and low temperatures found in deep ocean environments.
- Construction:
- Material Strength: Construction materials, such as concrete, steel, and composites, are tested for their ability to endure environmental stresses, including temperature fluctuations, moisture, and UV exposure. This ensures the longevity and safety of buildings and infrastructure.
- Weather Resistance: Testing for resistance to wind, rain, and extreme weather conditions ensures that buildings and structures can withstand environmental challenges.
- Consumer Products:
- Quality Assurance: Everyday consumer products, from home appliances to outdoor gear, are tested to ensure they can withstand typical environmental conditions they might encounter, such as temperature changes, humidity, and physical impacts.
- Customer Satisfaction: Environmental testing helps enhance product durability and reliability, leading to higher customer satisfaction and brand loyalty.
Environmental Testing Standards and Regulations
Environmental testing standards and regulations are essential frameworks that guide how products are tested for their ability to withstand various environmental conditions.
These standards ensure that products meet required performance, safety, and reliability criteria, promoting consistency and quality across industries.
Here’s an overview of key environmental testing standards and regulations:
Overview of Key Standards:
MIL-STD (Military Standards):
- MIL-STD-810: This standard defines test methods and procedures for evaluating the environmental effects on military equipment. It covers temperature extremes, humidity, vibration, shock, and more, ensuring that military hardware can operate reliably in harsh environments.
- MIL-STD-461: Specifies requirements for electromagnetic compatibility (EMC) testing, ensuring that electronic devices do not emit excessive interference and are resilient to external electromagnetic disturbances.
IEC (International Electrotechnical Commission):
- IEC 60068: This standard includes a series of test methods to assess the environmental conditions that electrical and electronic equipment may encounter. It covers temperature, humidity, vibration, shock, and other environmental factors.
- IEC 60529: Defines the Ingress Protection (IP) ratings for products, indicating their resistance to dust and water ingress.
ASTM International (formerly American Society for Testing and Materials):
- ASTM D4169: Provides guidelines for the performance testing of packages, including their ability to withstand vibrations, shocks, and other stresses during transportation.
- ASTM B117: Specifies the salt spray (fog) test for evaluating the corrosion resistance of materials and coatings.
ISO (International Organization for Standardization):
- ISO 9001: While not specific to environmental testing, ISO 9001 sets out quality management system requirements that include the need for effective testing and validation procedures.
- ISO 17025: Specifies general requirements for the competence of testing and calibration laboratories, ensuring accurate and reliable environmental testing results.
Importance of Compliance:
- Ensures Product Reliability: Compliance with these standards ensures that products are tested under consistent and recognized conditions, leading to reliable and predictable performance.
- Regulatory Requirements: Many industries have specific regulations that require adherence to these standards. Compliance helps manufacturers meet legal and regulatory requirements, avoiding potential fines and legal issues.
- Market Access: Adhering to international standards can facilitate entry into global markets, as products that meet recognized standards are more likely to be accepted by international customers and regulatory bodies.
Applying Standards Across Industries:
- Aerospace and Defense: Standards like MIL-STD-810 are crucial for testing the durability and reliability of military and aerospace components under extreme conditions.
- Consumer Electronics: IEC 60068 and ASTM B117 are often used to ensure that electronics can withstand temperature fluctuations, humidity, and corrosion.
- Automotive: Standards such as ISO 16750 provide testing procedures for automotive components, ensuring they can endure various environmental conditions.
- Medical Devices: Compliance with ISO 13485 and IEC 60601 ensures that medical devices meet safety and performance requirements under environmental stress.
Challenges and Considerations:
- Keeping Up with Evolving Standards: Standards and regulations frequently evolve to address new technologies and environmental concerns. Manufacturers must stay updated with the latest requirements to ensure ongoing compliance.
- Customization of Testing Procedures: While standards provide a baseline, specific applications may require customized testing procedures to address unique environmental challenges.
Future Trends:
- Sustainability: Emerging standards and regulations increasingly focus on sustainability and environmental impact, encouraging the development of eco-friendly materials and practices.
- Digitalization: The integration of digital tools and technologies in testing and compliance processes is enhancing the accuracy and efficiency of environmental testing.
Conclusion
Environmental testing is a critical component of product development and quality assurance, ensuring that products can withstand the various challenges they might face in real-world conditions.
By simulating extreme temperatures, humidity, vibrations, shocks, and other environmental factors, manufacturers can identify potential weaknesses and make necessary improvements before products reach the market.
This proactive approach enhances product reliability, reduces the risk of failures, and ensures compliance with industry standards and regulations.
Across different industries, from aerospace and defense to consumer electronics and automotive, environmental testing plays a vital role in guaranteeing that products meet performance and safety requirements.
Adhering to established standards and regulations not only helps in maintaining quality and reliability but also facilitates market access and compliance with legal requirements.
As technology evolves and environmental conditions change, staying updated with the latest standards and testing methodologies will be essential for continued product success and innovation.
Embracing these practices not only fosters customer trust and satisfaction but also contributes to the overall safety and effectiveness of products in diverse environments.
In summary, environmental testing is more than just a procedural formality; it is a key element in delivering high-quality, dependable products that perform reliably under a wide range of conditions.
By investing in comprehensive environmental testing, manufacturers can ensure their products meet the highest standards of durability, performance, and customer satisfaction.