The rise of Industrial IoT (IIoT) has marked a new era in manufacturing, where digital connectivity and real-time data play a pivotal role in optimizing production processes. By integrating sensors, devices, and advanced analytics into industrial environments, IIoT enables manufacturers to monitor and control operations with unprecedented precision.
Among the key enablers of this transformation is wireless networking, which allows seamless communication between machines, systems, and humans, without the limitations of physical cables.
Wireless networking in IIoT has become essential for modern manufacturing, offering the flexibility and scalability needed to adapt to ever-changing market demands. It facilitates real-time data exchange, enabling manufacturers to make quicker, more informed decisions and optimize their operations.
From connecting remote sensors on factory floors to enabling advanced automation and predictive maintenance, wireless technologies are reshaping the landscape of manufacturing.
In this context, understanding the role of wireless networking in driving efficiency becomes crucial. It is not only about adopting cutting-edge technology but also about leveraging it to streamline processes, reduce costs, and create a more agile and responsive production environment.
As wireless networking continues to evolve, its impact on manufacturing is becoming more pronounced, making it a key driver of the future of industrial automation.
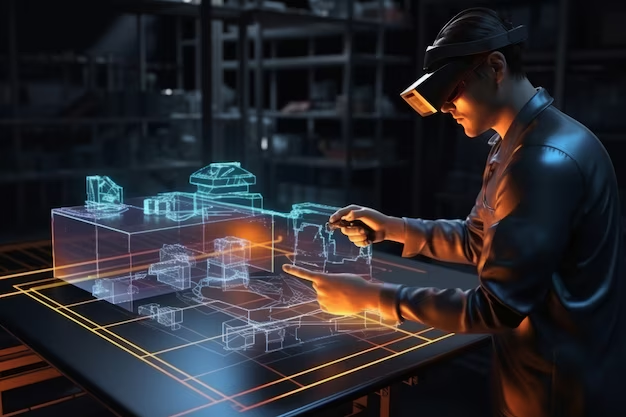
Understanding Wireless Networking in IIoT
Wireless networking serves as the backbone of Industrial IoT (IIoT) by providing the necessary infrastructure for seamless data transmission between connected devices and systems.
Unlike traditional wired solutions, wireless networks offer the flexibility to deploy sensors and devices across large industrial areas without the constraints of physical cabling. This makes them particularly valuable in dynamic manufacturing environments, where the need for real-time data and agile operations is paramount.
In the context of IIoT, wireless networking refers to the use of wireless communication technologies that connect various industrial devices—such as sensors, machines, controllers, and actuators—to centralized systems like edge servers or cloud platforms.
These connections facilitate the real-time flow of data, allowing manufacturers to monitor conditions, analyze performance metrics, and respond to changes quickly.
Several key wireless communication technologies are used in IIoT applications, each offering distinct advantages depending on the specific needs of the manufacturing environment:
- Wi-Fi (802.11): A widely used technology for high-speed data transmission over short to medium ranges. Wi-Fi is ideal for applications where devices require a strong and continuous connection to local networks, such as video surveillance systems or data-heavy sensors.
- Bluetooth and BLE (Bluetooth Low Energy): Known for their energy-efficient communication, Bluetooth and BLE are suitable for short-range connectivity between devices. BLE is often used in sensor networks where low power consumption is critical, making it a popular choice for monitoring equipment and environmental conditions in manufacturing facilities.
- Zigbee: A low-power, low-data-rate wireless standard that supports mesh networking, making it effective for connecting a large number of devices over a wide area. Zigbee is commonly used in industrial automation for applications like building control and remote monitoring.
- LoRaWAN (Long Range Wide Area Network): Known for its ability to transmit small amounts of data over long distances with minimal power consumption, LoRaWAN is ideal for connecting remote sensors and devices that need to operate in areas with limited network infrastructure. This makes it suitable for monitoring assets or conditions in expansive industrial spaces.
- 5G: As the next-generation mobile network, 5G offers low latency, high bandwidth, and massive device connectivity. It is particularly promising for IIoT applications that require real-time responsiveness, such as remote machine control and autonomous systems. 5G’s capabilities make it a game-changer for manufacturing, enabling more advanced automation and data-driven decision-making.
Wireless networking provides several advantages over wired solutions in industrial environments. It enables easier deployment and relocation of equipment, reduces the cost and complexity of cabling, and supports more dynamic and adaptable production setups. These benefits are especially valuable in smart factories that aim to integrate various technologies and adapt to evolving production requirements quickly.
Applications of Wireless Networking in Manufacturing
Wireless networking plays a crucial role in modern manufacturing, enabling a range of applications that drive efficiency, productivity, and innovation.
By connecting machines, sensors, and control systems without the need for physical cables, wireless technologies allow manufacturers to collect, analyze, and act on data in real-time, creating a more agile and responsive production environment.
Here are some key applications of wireless networking in manufacturing:
1. Real-Time Monitoring and Predictive Maintenance
- Wireless sensors placed on critical machinery can monitor parameters like temperature, vibration, pressure, and humidity continuously. These sensors transmit data to central systems, where it is analyzed to detect anomalies or signs of wear and tear.
- This real-time monitoring enables predictive maintenance, allowing manufacturers to address issues before they lead to costly breakdowns or unplanned downtime. For example, a factory could receive early alerts about abnormal vibrations in a motor, enabling maintenance teams to intervene before the equipment fails.
- This capability not only enhances equipment reliability but also extends the lifespan of machinery and reduces maintenance costs, contributing to overall operational efficiency.
2. Asset Tracking and Management
- Wireless networking simplifies asset tracking and inventory management in large manufacturing facilities. Using technologies like Bluetooth Low Energy (BLE) or RFID, manufacturers can keep track of the location and status of raw materials, finished products, and equipment in real time.
- This visibility helps to reduce losses, optimize inventory levels, and streamline logistics within the factory floor. For example, automated guided vehicles (AGVs) can use wireless networks to navigate around the factory and transport materials to the right location, reducing human intervention and improving the speed of material handling.
- In supply chain management, wireless connectivity also helps to improve transparency, allowing manufacturers to monitor the movement of products from the production line to delivery.
3. Energy Management and Optimization
- Effective energy management is critical for reducing operational costs and environmental impact in manufacturing. Wireless networking enables real-time monitoring of energy consumption across various systems and equipment, helping manufacturers to identify areas where energy use can be optimized.
- By integrating wireless sensors with energy management systems, manufacturers can track the energy usage of different machines, identify peak consumption periods, and implement strategies to reduce energy wastage.
- For example, wireless sensors can automatically adjust lighting, HVAC systems, and machinery settings based on real-time data, optimizing energy use according to production needs.
4. Automation and Control of Industrial Robots and Machinery
- Wireless networks play a significant role in enabling the automation of industrial robots and machinery. Through wireless communication, robots can receive instructions and exchange data with central control systems, allowing for more coordinated and efficient operations.
- For instance, in a smart factory, a network of wireless sensors can relay information about production line conditions to robotic arms, adjusting their operations in real time. This capability allows manufacturers to automate complex processes like assembly, packaging, and quality control, reducing labor costs and improving consistency.
- Additionally, wireless control systems can quickly reconfigure production lines to accommodate new product designs or changes in demand, enhancing the flexibility of manufacturing operations.
5. Enhancing Supply Chain Visibility
- Wireless connectivity extends beyond the factory floor, improving visibility across the entire supply chain. With the help of wireless sensors, manufacturers can track the movement and condition of goods throughout their journey from the supplier to the production facility and eventually to customers.
- This enhanced visibility helps manufacturers to maintain tighter control over inventory levels, reduce lead times, and respond more quickly to changes in customer demand. For example, wireless temperature sensors can monitor the conditions of perishable goods during transit, ensuring they remain within required temperature ranges and preventing spoilage.
- In addition, wireless communication between vehicles and logistics management platforms enables real-time tracking of deliveries, providing accurate delivery times and improving customer satisfaction.
Driving Efficiency through Wireless Connectivity
Wireless connectivity is a powerful catalyst for improving operational efficiency in the manufacturing sector. By enabling seamless communication between machines, systems, and personnel, wireless technologies facilitate faster decision-making, reduce operational costs, and enhance the flexibility of production processes. Here’s how wireless networking is driving efficiency in modern manufacturing:
1. Reducing Downtime with Real-Time Alerts
- One of the primary benefits of wireless networking is its ability to provide real-time data about the status and performance of machinery and equipment. Wireless sensors continuously monitor critical parameters like temperature, pressure, and vibration, and transmit this data to centralized systems.
- In the event of a potential issue, such as an overheating motor or a sudden drop in pressure, the system can instantly send alerts to maintenance teams. These real-time notifications allow for rapid intervention before minor issues escalate into major failures.
- This proactive approach to maintenance not only minimizes equipment downtime but also extends the lifespan of machinery, ensuring that production lines remain operational and efficient.
2. Optimizing Resource Utilization with Data-Driven Insights
- Wireless connectivity enables manufacturers to gather large volumes of data from various points across the production floor, creating a holistic view of operations. By analyzing this data, manufacturers can gain valuable insights into resource utilization, identifying inefficiencies and opportunities for optimization.
- For example, data from wireless sensors can reveal trends in energy consumption, allowing manufacturers to adjust their processes and reduce energy waste during low-demand periods. Similarly, monitoring production rates and material usage in real time can help optimize the scheduling of raw materials and reduce inventory carrying costs.
- This data-driven approach to resource management helps manufacturers operate with greater precision, reducing waste and maximizing the use of available resources.
3. Enhancing Flexibility and Scalability in Production Lines
- Wireless networks offer unmatched flexibility in reconfiguring production lines and adjusting to changing production requirements. Unlike wired systems, which are costly and time-consuming to modify, wireless solutions can be easily adapted to new layouts and processes.
- This flexibility is particularly valuable in industries where product designs and customer demands are constantly evolving. Manufacturers can quickly reprogram wireless-enabled machines or move sensors and equipment to new positions on the production floor, allowing them to adapt to new production runs without significant downtime.
- Additionally, as manufacturers expand their operations, wireless networks make it easier to scale up by adding new sensors, machines, or robotic systems without needing extensive infrastructure changes. This scalability enables manufacturers to grow their operations while maintaining efficiency.
4. Enabling Seamless Communication and Collaboration
- Wireless networking facilitates better communication between various stakeholders in the manufacturing process, including operators, managers, and maintenance personnel. With wireless connectivity, real-time data and insights can be shared across different departments and locations, enabling faster collaboration and decision-making.
- For example, if a machine experiences a sudden fault, maintenance teams can receive instant notifications, while production managers can adjust schedules to minimize the impact on output. This ability to coordinate responses quickly ensures that production processes continue smoothly, even when unexpected issues arise.
- Moreover, wireless connectivity can support the use of mobile devices and tablets, allowing workers to access data and control systems from anywhere on the factory floor. This mobility boosts efficiency by enabling workers to monitor and manage production processes without being tied to a fixed workstation.
5. Case Studies: Real-World Examples of Efficiency Gains
- Many manufacturers have already seen significant improvements in efficiency through the implementation of wireless networking. For example, a large automotive manufacturer reduced its maintenance costs by 20% after deploying a wireless sensor network to monitor critical equipment in real time, leading to fewer breakdowns and shorter repair times.
- Similarly, a food processing plant integrated wireless temperature sensors throughout its facility to ensure that products remained within optimal temperature ranges. This reduced spoilage and improved product quality, ultimately leading to cost savings and increased customer satisfaction.
- These examples illustrate the tangible benefits of adopting wireless networking in manufacturing, demonstrating how it can lead to better outcomes, from improved machine reliability to enhanced product quality.
Challenges and Solutions in Implementing Wireless Networking for IIoT
While wireless networking offers numerous advantages in Industrial IoT (IIoT), the implementation of these technologies in manufacturing environments is not without challenges. Factors such as interference, security, and compatibility can create obstacles that must be carefully managed to ensure successful deployment. However, with the right strategies and solutions, manufacturers can overcome these challenges and harness the full potential of wireless networking in IIoT. Here are some of the most common challenges and the solutions to address them:
1. Interference and Signal Reliability
- Challenge: Manufacturing environments often have a high concentration of machinery, metal structures, and electronic devices, which can interfere with wireless signals and reduce the reliability of communication networks. This interference can lead to data packet losses, delays, or complete signal disruptions, compromising the effectiveness of wireless monitoring and control.
- Solution: To mitigate interference, manufacturers can use frequency hopping techniques and spread-spectrum technologies like Zigbee, which are designed to be more resilient in environments with signal interference. Additionally, using directional antennas and signal repeaters can help strengthen signals over long distances and around obstacles. Selecting the right frequency band, such as 5 GHz instead of the more congested 2.4 GHz, can also minimize interference in densely packed environments.
2. Data Security and Privacy Concerns
- Challenge: Wireless networks in industrial settings are vulnerable to cyber threats such as unauthorized access, data interception, and malicious attacks. Since IIoT systems often transmit sensitive data related to production processes and machinery, a security breach could lead to significant disruptions and potential data loss.
- Solution: Implementing strong encryption protocols like WPA3 and VPNs (Virtual Private Networks) for secure communication can help protect data transmitted over wireless networks. Device authentication methods, such as digital certificates and two-factor authentication, add another layer of security by ensuring that only authorized devices can access the network. Additionally, regular network monitoring and security audits can help identify vulnerabilities and respond to potential threats before they escalate.
3. Integration with Legacy Systems
- Challenge: Many manufacturing facilities have a mix of modern and legacy equipment that may not natively support wireless communication. Integrating wireless networking with these older systems can be complex and may require significant modifications or replacements.
- Solution: To address compatibility issues, manufacturers can use wireless gateways and protocol converters that bridge the communication gap between legacy systems and modern wireless networks. These devices translate data from older equipment into protocols compatible with wireless networks, allowing manufacturers to retain their existing investments while still benefiting from wireless connectivity. Additionally, edge computing solutions can be deployed to process data from legacy systems locally before transmitting it to centralized platforms.
4. Network Scalability and Bandwidth Management
- Challenge: As manufacturers scale their IIoT deployments, the number of connected devices and data traffic increases, which can strain wireless network capacity. This can result in network congestion, reduced bandwidth availability, and slower data transmission, affecting real-time decision-making and overall system performance.
- Solution: Mesh networking can be an effective solution for scalability, as it allows devices to communicate directly with each other, creating a self-healing network that adjusts to changes in the environment. Quality of Service (QoS) mechanisms can be implemented to prioritize critical data, such as control commands or safety alerts, over less time-sensitive information. Additionally, leveraging 5G technology can provide the high bandwidth and low latency required to support large-scale IIoT deployments, making it easier to accommodate future growth.
5. Power Management for Wireless Devices
- Challenge: Many wireless devices, especially those placed in remote or hard-to-reach areas, rely on battery power for operation. Frequent battery replacements or recharges can be costly and labor-intensive, creating maintenance challenges for manufacturers.
- Solution: To extend the battery life of wireless devices, manufacturers can use low-power communication protocols like Bluetooth Low Energy (BLE) or LoRaWAN, which are designed to transmit data with minimal energy consumption. Additionally, energy harvesting techniques, such as solar panels or vibration energy harvesters, can provide a supplementary power source for remote sensors, reducing the need for manual battery replacement. Implementing adaptive data transmission intervals, where devices send data less frequently during periods of low activity, can also conserve power.
6. Latency Concerns in Real-Time Applications
- Challenge: In applications where real-time responsiveness is critical—such as remote machine control, safety systems, or automated assembly lines—latency in wireless networks can be a significant issue. Delays in data transmission can impact the speed and accuracy of these systems, leading to potential errors or safety risks.
- Solution: To reduce latency, manufacturers can use edge computing to process data closer to the source, minimizing the time it takes for data to travel back and forth between devices and central servers. Private 5G networks offer another solution, providing dedicated high-speed, low-latency connectivity for time-sensitive industrial applications. By deploying local wireless access points and reducing network hops, manufacturers can ensure faster data communication and smoother operation of real-time systems.
7. High Initial Investment and ROI Concerns
- Challenge: Implementing wireless networking for IIoT can involve a significant initial investment in hardware, software, and infrastructure upgrades. This can make it difficult for manufacturers, particularly small and medium enterprises, to justify the costs without a clear understanding of the return on investment (ROI).
- Solution: To ensure a positive ROI, manufacturers should start with pilot projects that focus on high-impact areas, such as predictive maintenance or energy optimization, before scaling up. This allows them to demonstrate the benefits and cost savings of wireless networking in a controlled environment. Partnering with technology providers and IIoT consultants can help streamline the implementation process, ensuring that investments align with long-term strategic goals. Furthermore, leveraging modular wireless solutions allows manufacturers to gradually expand their capabilities as their needs evolve.
Conclusion
The integration of wireless networking in Industrial IoT represents a transformative shift in manufacturing, unlocking new levels of efficiency and operational excellence. By enabling real-time communication between machines, systems, and personnel, wireless technologies empower manufacturers to optimize processes, reduce downtime, and enhance resource utilization. Despite the challenges associated with implementing wireless solutions, such as interference, security, and integration with legacy systems, manufacturers can adopt targeted strategies to overcome these obstacles. The successful deployment of wireless networking not only drives productivity but also fosters a more agile and responsive manufacturing environment.
As industries continue to embrace digital transformation, the role of wireless networking in IIoT will become increasingly vital. Manufacturers who proactively address the challenges and leverage the benefits of wireless connectivity will position themselves for success in a rapidly evolving marketplace. By harnessing the power of data-driven insights and real-time collaboration, they can ensure a competitive edge, enhance operational resilience, and pave the way for innovative manufacturing practices that meet the demands of the future. Embracing these advancements will be key to thriving in the digital age of manufacturing.