The electric vehicle (EV) revolution is transforming the global automotive industry, driving the shift towards cleaner, more sustainable transportation. However, as EVs become more prevalent, their power management systems face increasing demands for efficiency, reliability, and innovation.
Managing power consumption in electric vehicles is crucial, not only for optimizing battery life but also for ensuring overall vehicle performance, particularly in challenging environments and dynamic driving conditions.
This is where Field Programmable Gate Arrays (FPGAs) come into play. FPGAs, known for their versatility and real-time processing capabilities, have emerged as a key enabler of advanced power management systems in EVs.
These devices offer the flexibility to implement complex, energy-efficient algorithms and adaptive control systems that allow EV manufacturers to optimize power usage in critical areas like battery management, thermal control, and motor efficiency.
In this blog, we will explore the pivotal role of FPGA technology in enhancing power management systems within electric vehicles, diving into the challenges it addresses, the specific techniques it enables, and its growing influence in the future of EV design.
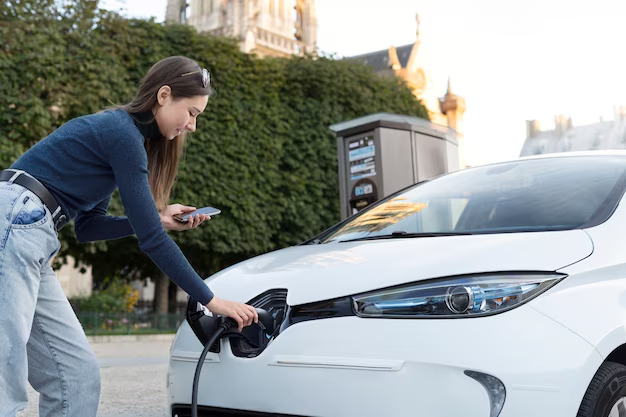
Challenges in Power Management for Electric Vehicles
Power management in electric vehicles (EVs) is a critical factor that directly influences their performance, efficiency, and overall adoption.
As EV technology advances, the complexity of managing power becomes more pronounced due to a variety of challenges that arise in areas such as battery performance, energy distribution, and vehicle dynamics. Below are some of the key challenges:
1. Battery Efficiency and Longevity
- Battery Degradation:
One of the most significant challenges in EVs is ensuring that the battery maintains its efficiency over time. Batteries degrade due to factors like overcharging, deep discharges, and excessive heating, reducing their lifespan and overall efficiency. - Energy Density:
Limited battery capacity (energy density) directly impacts the vehicle’s range. Efficient power management systems are needed to maximize the available energy without sacrificing performance.
2. Real-Time Energy Distribution
- Dynamic Power Demands:
EVs operate under varying conditions that create dynamic power demands. Factors like acceleration, regenerative braking, heating, and cooling require quick adjustments in power allocation. - Optimal Power Flow:
Distributing power efficiently between different systems—such as propulsion, heating/cooling, and auxiliary systems—requires real-time control. Inconsistent or inefficient power flow can lead to wasted energy and reduced performance.
3. Thermal Management
- Excessive Heat Generation:
EV components, especially batteries, inverters, and motors, generate significant heat during operation. Without proper thermal management, excessive heat can reduce the efficiency of the power systems, cause safety concerns, and accelerate wear on key components. - Cooling Systems Power Consumption:
Managing the vehicle’s temperature efficiently without significantly increasing power consumption is a delicate balance. Cooling systems must be optimized to minimize energy use while protecting sensitive components from overheating.
4. Regenerative Braking Efficiency
- Maximizing Energy Recovery:
Regenerative braking systems, which capture kinetic energy and convert it back into stored electrical energy, play a crucial role in extending the driving range. However, managing this energy recovery efficiently is challenging, particularly in varied driving conditions where power needs fluctuate rapidly. - Losses in Conversion:
The process of converting and storing energy during regenerative braking is not always efficient, leading to losses that must be minimized through advanced power management techniques.
5. Battery Charging and Grid Integration
- Fast Charging Challenges:
Fast charging systems provide convenience but present challenges in managing power flow without straining the battery. Rapid charging cycles, if not properly managed, can accelerate battery degradation and cause thermal issues. - Grid Overload and Stability:
Integrating electric vehicles with the power grid for charging introduces another layer of complexity. Poorly managed charging could lead to grid overload, requiring careful coordination between EV charging infrastructure and grid power availability.
6. Energy Efficiency in Auxiliary Systems
- Balancing Power for Auxiliary Functions:
While propulsion is the primary consumer of power in EVs, auxiliary systems such as lighting, infotainment, and climate control also draw significant amounts of energy. Efficient power management must ensure that these systems operate optimally without draining battery reserves excessively. - Idle Power Consumption:
Managing power consumption when the vehicle is idle or in standby mode is equally important. Reducing unnecessary power draw during these states can extend the overall battery life and range.
7. Scalability and Adaptability of Power Management Systems
- Varying Requirements Across EV Models:
Power management systems must be adaptable to different EV configurations, from compact cars to heavy-duty electric trucks. This scalability requires flexible systems capable of optimizing power usage based on the unique demands of each vehicle type. - Future-Proofing for New Technologies:
As electric vehicle technology evolves, power management systems must remain adaptable to accommodate new innovations, such as wireless charging, vehicle-to-grid (V2G) systems, and advanced driver assistance systems (ADAS). This requires a highly configurable and scalable power management solution.
Why FPGAs are Ideal for Power Management in EVs
Field Programmable Gate Arrays (FPGAs) are increasingly becoming a key technology in addressing the power management challenges faced by electric vehicles (EVs). Their inherent flexibility, parallel processing capability, and adaptability to complex, real-time applications make them a perfect fit for optimizing energy consumption in electric vehicles. Below are several reasons why FPGAs are particularly well-suited for power management in EVs:
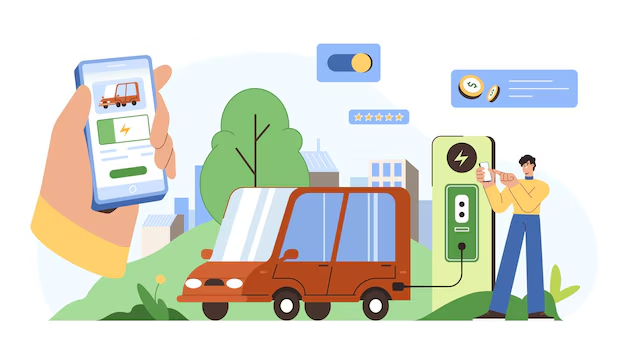
1. Real-Time Processing Capabilities
- Immediate Response to Power Fluctuations:
One of the key benefits of FPGAs is their ability to process data in real-time, which is crucial for managing power in dynamic driving environments. Whether it’s monitoring battery health, controlling power distribution between different vehicle systems, or managing regenerative braking, FPGAs can instantly respond to fluctuations in power demand and supply. - Precision Control:
FPGAs provide precise control over power distribution in critical EV systems. They can adjust voltage levels, frequencies, and power flow with high accuracy, ensuring that power is used as efficiently as possible, minimizing waste.
2. Parallel Processing for Complex Tasks
- Simultaneous Management of Multiple Systems:
EVs rely on multiple subsystems, such as propulsion, battery management, heating/cooling, and infotainment, all requiring different levels of power at different times. FPGAs are designed to handle parallel processing, allowing them to manage multiple tasks concurrently without bottlenecks. This capability is crucial for balancing power between subsystems without compromising performance. - Increased Efficiency in Power Distribution:
By processing many tasks simultaneously, FPGAs can optimize energy use across various vehicle components, helping to reduce overall power consumption and extend battery life.
3. Flexibility and Reconfigurability
- Adaptability to Changing Requirements:
Unlike traditional microcontrollers or ASICs (Application-Specific Integrated Circuits), FPGAs are highly flexible and can be reprogrammed after deployment. This flexibility allows automotive engineers to update or modify power management algorithms as technology evolves or new energy-saving techniques are developed. This is especially important in an industry where rapid innovation is essential to staying competitive. - Future-Proofing EV Systems:
As EV technology progresses and new power management strategies emerge, FPGAs can be reconfigured to incorporate these advancements without requiring a complete hardware overhaul. This reconfigurability ensures that FPGAs remain relevant for the long-term lifecycle of EVs.
4. Low Power Consumption
- Energy-Efficient Processing:
FPGAs themselves consume relatively low power compared to traditional CPUs and GPUs, making them an ideal choice for applications where energy efficiency is paramount. Their ability to manage power consumption dynamically further improves their suitability for energy-conscious applications in EVs. - Optimized Sleep and Wake Modes:
FPGAs are also capable of optimizing power in different operating modes, such as when the vehicle is idle or in sleep mode. They can intelligently control the power state of different subsystems, ensuring minimal energy draw when full performance is not required.
5. Customizable Power Management Algorithms
- Tailored Power Management Solutions:
With FPGAs, automakers can design and implement custom power management algorithms tailored to the specific needs of their vehicles. Whether it’s adjusting power flow based on the driving environment, controlling battery temperature, or enhancing regenerative braking systems, FPGAs offer a level of customization that is difficult to achieve with off-the-shelf processors. - Integration with Machine Learning for Predictive Power Management:
FPGAs can be programmed to support machine learning algorithms, allowing EVs to predict power demands based on driving behavior, environmental conditions, or traffic patterns. This predictive approach helps to optimize power usage even further, ensuring maximum efficiency in all situations.
6. Scalability Across Different EV Models
- From Compact Cars to Heavy-Duty Trucks:
FPGAs are highly scalable and can be utilized across various EV models, from small urban vehicles to large commercial trucks. This versatility is critical in an automotive industry where power management requirements vary significantly depending on the size and purpose of the vehicle. FPGAs allow for scalable solutions that can be tailored to the specific power needs of each model. - Integration with Existing Automotive Systems:
FPGAs can be seamlessly integrated into existing automotive electronic control units (ECUs) and power management systems, ensuring compatibility and enhancing the efficiency of the overall system without requiring drastic changes in architecture.
7. Support for Advanced Power-Saving Technologies
- Dynamic Voltage and Frequency Scaling (DVFS):
FPGAs are well-suited for implementing DVFS, which adjusts the voltage and frequency of the processor based on real-time performance requirements. By lowering the voltage or frequency when the system is under low load, FPGAs can reduce power consumption without affecting performance. - Energy Recovery and Storage Management:
FPGAs can be used to enhance the efficiency of regenerative braking systems, helping to maximize energy recovery and manage how that energy is stored and utilized within the vehicle. This helps extend the driving range while improving overall energy efficiency.
FPGA-Based Power Optimization Techniques in EVs
Field Programmable Gate Arrays (FPGAs) offer a versatile platform for implementing advanced power optimization techniques in electric vehicles (EVs). Their ability to execute multiple processes simultaneously and adapt to changing conditions in real time makes them ideal for enhancing energy efficiency across various vehicle systems. Below are some of the key FPGA-based power optimization techniques employed in EVs:
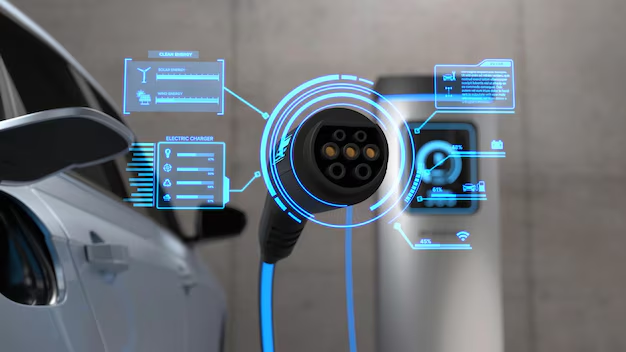
1. Dynamic Voltage and Frequency Scaling (DVFS)
- Optimizing Power Based on Load:
Dynamic Voltage and Frequency Scaling (DVFS) is a technique where the voltage and frequency of the processor are adjusted according to the system’s current load. FPGAs can dynamically alter these parameters in real-time, ensuring that the system operates with minimal energy consumption during low-load conditions and ramps up when higher performance is needed. - Benefits for EVs:
In electric vehicles, this technique is critical for subsystems like the battery management system (BMS), motor control units, and infotainment systems. By reducing voltage and frequency during periods of low demand, power usage is minimized, contributing to extended battery life and increased driving range.
2. Parallel Processing for Efficient Resource Allocation
- Simultaneous Control of Multiple Systems:
FPGAs excel at handling parallel tasks, allowing them to manage multiple subsystems in an EV simultaneously. For instance, they can control power distribution between propulsion, regenerative braking, and auxiliary systems such as lighting or climate control, all at the same time. - Reducing Bottlenecks:
With parallel processing, FPGAs optimize power usage by eliminating bottlenecks in the system. This leads to more efficient power allocation and better overall vehicle performance, especially in situations requiring rapid adjustments in power distribution, like acceleration or braking.
3. Adaptive Power Management Algorithms
- Real-Time Adjustments Based on Driving Conditions:
FPGAs allow automakers to implement adaptive power management algorithms that can react to real-time conditions. For example, FPGAs can adjust power distribution based on factors like road conditions, driving style, or weather. These adaptive algorithms ensure that the power usage is optimized based on current requirements, reducing unnecessary power draw and improving overall energy efficiency. - Customizable Power Profiles:
FPGA-based systems can be programmed to implement customizable power profiles that change depending on the vehicle’s mode (e.g., eco, sport, or normal). This ensures that power is only used where and when it is needed, further extending battery life and improving driving range.
4. Energy Recovery and Regenerative Braking Optimization
- Maximizing Energy Recovery Efficiency:
Regenerative braking is a critical energy-saving feature in EVs, capturing kinetic energy and converting it back into electrical energy that can be stored in the battery. FPGAs can optimize this process by managing the timing and intensity of energy capture, ensuring minimal energy loss during conversion. - Precise Control Over Energy Storage:
FPGAs can control how the recovered energy is distributed to the battery, ensuring that the charging process is efficient and does not cause unnecessary strain on the battery cells. This not only enhances the efficiency of the braking system but also helps extend battery life.
5. Thermal Management Optimization
- Monitoring and Controlling Heat Generation:
Power management in EVs also involves keeping the system’s components within optimal temperature ranges. FPGAs can be used to manage cooling systems, dynamically adjusting fan speeds or activating thermal management protocols based on real-time heat data. - Energy-Efficient Cooling Systems:
Instead of relying on fixed cooling patterns, FPGAs allow for a more energy-efficient approach by adjusting the cooling based on actual need, reducing power consumption by avoiding overcooling and ensuring consistent temperature regulation across key components like the battery and motor.
6. Predictive Power Management with Machine Learning
- Anticipating Power Demand:
FPGAs can be integrated with machine learning algorithms to predict future power requirements based on driving patterns, environmental conditions, or historical data. These predictive models enable proactive adjustments in power usage, ensuring the vehicle is prepared for upcoming energy demands while avoiding overconsumption. - Optimizing Power Based on Driving Habits:
For example, if the system detects that the driver frequently accelerates aggressively, it can adjust power distribution to optimize the battery and motor output during acceleration. Similarly, if the system predicts a heavy braking event, it can adjust regenerative braking settings to maximize energy recovery.
7. Battery Management System (BMS) Optimization
- Real-Time Battery Health Monitoring:
The Battery Management System (BMS) is crucial in ensuring the battery’s health and efficiency. FPGAs provide a platform to monitor various battery parameters such as voltage, temperature, and state of charge (SOC) in real-time. This enables precise control over charging and discharging cycles, reducing the risk of overcharging or deep discharges. - Optimizing Battery Life and Performance:
By adjusting the power output based on real-time battery conditions, FPGAs help ensure that the battery operates within its optimal parameters. This not only maximizes battery performance during vehicle operation but also extends the overall lifespan of the battery by avoiding conditions that can accelerate degradation.
8. Motor Control and Inverter Optimization
- Efficient Motor Control:
Electric motors are among the largest consumers of power in EVs, making motor control a key area for optimization. FPGAs can be used to implement advanced motor control algorithms, such as Field-Oriented Control (FOC), which adjusts the motor’s torque and speed to minimize energy consumption without sacrificing performance. - Inverter Optimization:
In addition to motor control, FPGAs can optimize the performance of inverters, which convert the battery’s DC power into the AC power used by the motor. By dynamically adjusting the inverter’s switching patterns, FPGAs reduce power losses and enhance overall system efficiency.
9. Power-Saving Modes for Idle and Low-Load Conditions
- Minimizing Power Draw in Idle States:
FPGAs allow for the implementation of low-power or sleep modes when the vehicle is idle, reducing unnecessary power consumption. These modes can be activated when the vehicle is at a stoplight or during traffic, helping to conserve battery energy during periods of inactivity. - Efficient Management of Auxiliary Systems:
Even when the vehicle is not in motion, auxiliary systems such as lighting, infotainment, and climate control continue to consume power. FPGAs manage these systems efficiently by lowering their power usage when full performance is not required, further contributing to overall energy savings
Advantages of Using FPGAs for Power Management in EVs
FPGAs (Field Programmable Gate Arrays) offer several unique advantages when applied to power management in electric vehicles (EVs). Their flexibility, real-time processing capabilities, and adaptability make them a powerful tool for optimizing energy consumption in a wide range of EV systems. Here are the key advantages of using FPGAs for power management in electric vehicles:
1. Real-Time Processing and Control
- Immediate Response to Power Demands:
One of the biggest advantages of FPGAs is their ability to perform real-time processing. This capability allows EVs to make instant adjustments to power usage based on driving conditions, road terrain, battery health, and vehicle load, which is crucial for optimizing energy efficiency and performance.- Example: In fast-changing situations like acceleration or regenerative braking, FPGAs can rapidly adjust the power distribution to the motor or battery, ensuring that energy is used efficiently without delays.
2. Parallel Processing for Multi-System Control
- Simultaneous Management of Multiple Systems:
FPGAs are designed to handle parallel processes, allowing them to control and monitor various vehicle subsystems at the same time. This includes the motor, battery, cooling systems, and auxiliary systems, all of which need to work together efficiently to optimize power consumption.- Example: In an EV, FPGAs can manage power distribution between propulsion and other systems like climate control or infotainment, ensuring balanced power usage without sacrificing performance in any area.
3. Energy Efficiency and Low Power Consumption
- Optimized for Power-Sensitive Applications:
FPGAs consume relatively low power compared to traditional processors. They can be tailored to the specific power management needs of an EV, ensuring that no excess energy is consumed during operations. This efficiency is particularly important in EVs, where every watt of power saved can extend the vehicle’s range.- Example: FPGAs can be programmed to enter low-power modes during idle or low-demand situations, minimizing unnecessary power consumption.
4. Flexibility and Reconfigurability
- Adaptability to Evolving Power Management Requirements:
Unlike traditional ASICs (Application-Specific Integrated Circuits), FPGAs are highly reconfigurable. This allows manufacturers to update or change power management strategies after the vehicle has been deployed. As new power optimization techniques or algorithms are developed, the FPGA-based system can be reprogrammed to incorporate these improvements without needing hardware changes.- Example: As battery technology evolves, new charging and discharging methods can be programmed into the FPGA, ensuring that the EV always operates with the most efficient power management strategies.
5. Enhanced Precision and Customization
- Tailored Power Management Algorithms:
FPGAs offer a high degree of precision in power control. They allow for the implementation of customized power management algorithms that can be tailored to specific vehicle models, battery types, and driving conditions. This precision helps ensure that the vehicle operates within its optimal power range, reducing energy waste and extending battery life.- Example: FPGAs can implement specific voltage and frequency scaling techniques customized to the EV’s motor and battery characteristics, achieving fine-tuned power control.
6. Scalability for Different EV Models
- Applicable Across a Range of Vehicles:
FPGAs are scalable and can be configured for different types of electric vehicles, from compact city cars to heavy-duty electric trucks. This scalability makes them a versatile choice for manufacturers looking to optimize power management across various EV models with differing power needs.- Example: The same FPGA architecture can be used to manage power in both a small electric vehicle and a large commercial EV by simply reconfiguring the programming based on the power requirements of each.
7. Improved Thermal Management
- Dynamic Thermal Control:
FPGAs are capable of monitoring and managing thermal conditions in real time. This capability is critical in electric vehicles, where overheating of the battery, motor, or other power-intensive components can lead to efficiency losses and reduced lifespan. By controlling cooling systems dynamically, FPGAs ensure that only the necessary amount of energy is spent on thermal management.- Example: FPGAs can adjust the cooling fan speeds or activate thermal management protocols only when necessary, preventing energy wastage from overcooling.
8. Support for Advanced Power Management Algorithms
- Integration of AI and Machine Learning:
FPGAs can integrate advanced power management algorithms, including those based on AI and machine learning, which allow the system to learn from previous driving patterns and predict future power demands. These algorithms can be continuously updated to ensure the EV operates at peak efficiency under varying conditions.- Example: An FPGA in an EV can learn a driver’s habits, such as frequent acceleration, and adjust power management strategies accordingly to optimize energy usage without manual intervention.
9. High Reliability and Longevity
- Robust Design for Automotive Applications:
FPGAs are known for their robustness and reliability, which are crucial in the automotive industry. They are designed to handle the harsh conditions of automotive environments, including extreme temperatures, vibration, and electromagnetic interference. This reliability ensures that the EV’s power management system operates effectively over the vehicle’s lifetime.- Example: FPGAs used in EVs can withstand temperature variations and heavy workloads, ensuring stable performance in all weather conditions and terrain types.
10. Fast Prototyping and Time-to-Market
- Accelerating EV Development:
FPGAs enable rapid prototyping, allowing automakers to test and refine power management systems quickly. This reduces the time-to-market for new electric vehicle models, as FPGAs can be programmed, tested, and adjusted faster than designing custom ASICs.- Example: Automakers can use FPGAs to prototype and test different power management algorithms during the vehicle’s development phase, speeding up the overall development cycle.
Conclusion
FPGAs provide a transformative solution for power management in electric vehicles, offering the flexibility, real-time processing, and energy efficiency necessary to meet the evolving demands of EV technology. Their ability to handle multiple systems simultaneously, adjust to changing conditions in real time, and support advanced power optimization algorithms make FPGAs an ideal choice for automakers striving to enhance EV performance and efficiency. As electric vehicles continue to grow in popularity, the use of FPGAs in power management will be critical to advancing innovations, extending vehicle range, and improving overall energy efficiency. With their adaptability and scalability, FPGAs will remain at the forefront of power management solutions, helping drive the future of sustainable and efficient electric mobility.