In today’s rapidly evolving industrial landscape, automation systems are becoming more advanced, interconnected, and power-intensive. From robotic assembly lines to precision control systems, industrial automation relies heavily on electrical energy to maintain efficiency, accuracy, and productivity. However, with rising energy costs and growing environmental concerns, industries are under increasing pressure to optimize power consumption while maintaining high operational standards.
Energy-efficient power conversion plays a crucial role in addressing these challenges. By improving the efficiency of converting electrical energy from one form to another, industries can significantly reduce energy losses, lower operational costs, and contribute to global sustainability efforts. Efficient power conversion not only enhances the performance of automation systems but also extends the lifespan of equipment, minimizes heat dissipation, and ensures compliance with stringent energy regulations.
This article explores the key aspects of energy-efficient power conversion in industrial automation systems, including the latest technologies, design strategies, and future trends. By adopting advanced power conversion techniques, industries can achieve both economic and environmental benefits, paving the way for a smarter and greener manufacturing future.

Understanding Power Conversion in Industrial Automation
Basics of Power Conversion
Industrial automation systems require a reliable and efficient power supply to operate machinery, sensors, controllers, and communication networks. Power conversion is the process of transforming electrical energy from one form to another to meet the specific voltage, current, and frequency requirements of industrial equipment. This process ensures stable operation, protects sensitive electronics, and enhances overall system efficiency.
There are three primary types of power conversion used in industrial automation:
- AC to DC Conversion (Rectification): Converts alternating current (AC) from the main power supply into direct current (DC), which is required by automation controllers, embedded systems, and variable frequency drives (VFDs).
- DC to DC Conversion (Voltage Regulation): Modifies DC voltage levels to match the power needs of different components within an automation system. Examples include step-up (boost) and step-down (buck) converters.
- DC to AC Conversion (Inversion): Converts stored DC power (from batteries or renewable energy sources) into AC power for operating industrial motors, pumps, and other machinery.
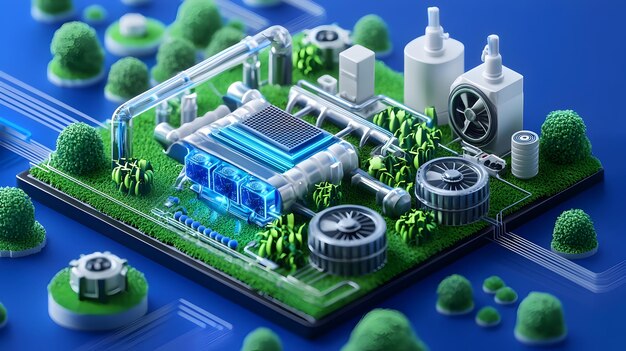
Role of Power Electronics in Automation Systems
Power electronics form the backbone of industrial automation by ensuring efficient energy conversion and distribution. Key components used in power conversion include:
- Transformers and Rectifiers: Convert and regulate AC power for automation systems.
- Switching Devices (IGBTs, MOSFETs, SiC & GaN transistors): Improve efficiency by enabling high-speed switching with minimal energy loss.
- Power Supply Units (PSUs): Provide regulated power to automation controllers, sensors, and actuators.
- Energy Storage Systems (Supercapacitors, Batteries): Maintain power stability and reduce downtime in case of fluctuations or outages.
Key Challenges in Power Conversion for Industrial Automation
Despite advancements in power conversion technology, industries face several challenges in optimizing energy efficiency:
- Energy Losses: Traditional power conversion systems experience losses in the form of heat, reducing overall efficiency.
- Harmonics and Power Quality Issues: Poor power conversion can introduce electrical noise and distortions, affecting the performance of automation systems.
- Heat Dissipation and Thermal Management: Inefficient power conversion leads to excessive heat generation, which can damage components and increase cooling costs.
- System Complexity: As automation systems become more interconnected, integrating multiple power conversion stages efficiently becomes more challenging.
Technologies Driving Energy-Efficient Power Conversion
As industrial automation systems become more complex and power-intensive, advancements in power conversion technologies are essential for improving energy efficiency, reducing losses, and ensuring system reliability. Modern power conversion solutions integrate cutting-edge semiconductor materials, smart power management techniques, and energy recovery systems to optimize industrial operations.
Advanced Power Semiconductor Devices
Traditional silicon-based power electronics are being replaced or supplemented with new semiconductor technologies that offer higher efficiency and lower energy losses. Key innovations include:
- Silicon Carbide (SiC) and Gallium Nitride (GaN) Transistors: These wide bandgap semiconductors enable higher switching frequencies, lower heat dissipation, and reduced power losses, making them ideal for industrial automation applications.
- Insulated Gate Bipolar Transistors (IGBTs): Used in high-power applications such as motor drives and inverters, IGBTs provide fast switching capabilities with improved energy efficiency.
High-Efficiency Power Supply Units (PSUs)
Power supplies play a critical role in industrial automation by providing stable and regulated voltage to controllers, sensors, and actuators. Modern PSUs integrate:
- Switched-Mode Power Supplies (SMPS): Offer higher efficiency compared to traditional linear power supplies by reducing energy losses during voltage conversion.
- Digital Power Management: Intelligent power supply units that adjust voltage and current dynamically based on real-time load conditions, optimizing efficiency.
Smart Power Management Systems
With the rise of Industry 4.0 and AI-driven automation, smart power management is transforming industrial energy usage. Features include:
- AI and Machine Learning (ML) Optimization: AI algorithms analyze energy consumption patterns and adjust power delivery to reduce waste.
- Predictive Maintenance: Smart power management detects inefficiencies and potential failures in power conversion components, minimizing downtime.
- Dynamic Load Balancing: Ensures optimal power distribution across automation systems, preventing overloading and reducing energy losses.
Regenerative Energy Systems
Regenerative power conversion enables industries to recover and reuse excess energy instead of dissipating it as heat. Examples include:
- Regenerative Braking in Motor Drives: Captures kinetic energy from motors and feeds it back into the system, improving overall energy efficiency.
- Energy Recovery in Industrial HVAC and Cooling Systems: Converts waste heat into usable power, reducing cooling costs.
DC Microgrids for Industrial Automation
Many industries are transitioning towards DC microgrids, which offer improved energy efficiency over traditional AC power distribution. Benefits include:
- Direct Integration with Renewable Energy Sources: DC microgrids seamlessly connect with solar panels and battery storage systems, minimizing conversion losses.
- Reduced Energy Losses in Power Transmission: Eliminates multiple AC-DC-AC conversion stages, leading to higher overall efficiency.
- Improved Reliability and Scalability: DC microgrids support modular power distribution, making them ideal for flexible industrial setups.
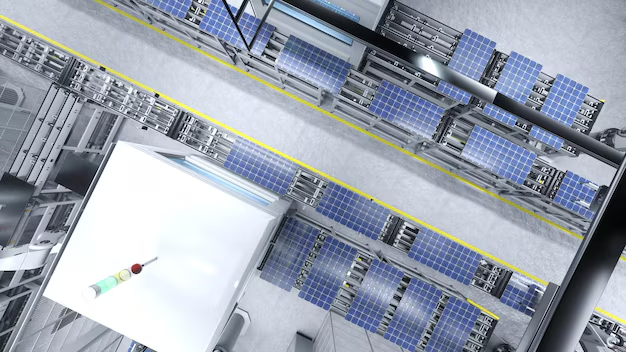
Role of Renewable Energy in Industrial Automation
The integration of renewable energy into industrial automation systems is transforming the way industries consume power. With increasing energy demands, rising electricity costs, and stringent environmental regulations, industries are shifting towards sustainable energy solutions to enhance efficiency and reduce their carbon footprint. Renewable energy sources such as solar, wind, and hybrid energy systems are playing a crucial role in ensuring energy security and optimizing automation processes.
Integration of Renewable Energy Sources
Industries are leveraging renewable energy in multiple ways to support their automation infrastructure:
Solar Power for Industrial Automation
- On-site Solar Panels: Many industries install rooftop or ground-mounted solar panels to generate electricity for automation systems, reducing dependence on the grid.
- Direct DC Power Supply: Solar panels produce DC power, which can be directly utilized in DC microgrids, minimizing conversion losses.
- Hybrid Solar-Grid Systems: A combination of solar power and grid electricity ensures uninterrupted operation, even during low sunlight conditions.
Wind Energy for Industrial Automation
- Industrial Wind Turbines: Many large-scale industries deploy wind turbines to generate power for automation processes.
- Energy Storage and Grid Support: Wind energy can be stored in battery systems or used in combination with grid electricity to maintain a stable power supply.
Hydropower and Other Renewable Sources
- Small-Scale Hydropower: Some industries use hydroelectric systems to generate on-site renewable power, especially those located near water sources.
- Geothermal and Biomass Energy: Industries with high energy consumption are exploring alternative sources like geothermal and biomass for clean and consistent power generation.
Hybrid Energy Systems for Industrial Applications
To ensure a reliable and uninterrupted power supply, industries are adopting hybrid renewable energy systems that combine multiple energy sources. These systems provide:
- Enhanced Energy Availability: Solar power during the day, wind energy at night, and battery storage for backup ensure continuous power supply.
- Grid Independence: Industries can reduce dependency on traditional power grids, improving resilience against power outages.
- Optimized Energy Use: Smart energy management systems distribute power efficiently across automation systems, ensuring minimal wastage.
Battery Storage and Energy Harvesting Solutions
Since renewable energy generation fluctuates based on weather conditions, industries integrate energy storage and harvesting solutions to maintain consistent power availability:
- Lithium-Ion and Solid-State Batteries: Store excess renewable energy and supply power during peak automation loads.
- Supercapacitors: Provide rapid energy discharge for high-speed automation processes.
- Energy Harvesting Technologies: Convert mechanical vibrations, waste heat, and other energy forms into usable power for automation sensors and IoT devices.
Benefits of Renewable Energy in Industrial Automation
Integrating renewable energy into industrial automation systems offers several advantages:
- Cost Savings: Reduces electricity bills by utilizing free energy sources like sunlight and wind.
- Lower Carbon Footprint: Helps industries meet sustainability goals and comply with environmental regulations.
- Increased Energy Efficiency: Minimizes energy losses through direct DC power integration and smart energy management.
- Improved Reliability: Reduces dependency on grid power and ensures automation systems remain operational during outages.
Conclusion
Energy-efficient power conversion is transforming industrial automation by enabling sustainable, cost-effective, and high-performance operations. By integrating advanced power semiconductor devices, smart energy management systems, and renewable energy sources, industries can significantly reduce energy waste, lower operational costs, and enhance reliability. The adoption of DC microgrids, regenerative energy systems, and AI-driven power optimization ensures a seamless and efficient power supply, reducing dependency on traditional energy grids while improving overall productivity.
As industrial automation continues to evolve, future advancements in wide-bandgap semiconductors, AI-powered predictive energy management, and hybrid renewable energy systems will further enhance energy efficiency. Companies that proactively implement these innovations will gain a competitive edge by reducing carbon footprints, achieving sustainability goals, and ensuring long-term cost savings. By embracing energy-efficient power conversion technologies, industries can pave the way for a smarter, greener, and more efficient future.