Introduction
In the vast expanse of the aerospace industry, where precision and reliability are paramount, the role of test and measurement stands as an indispensable pillar.
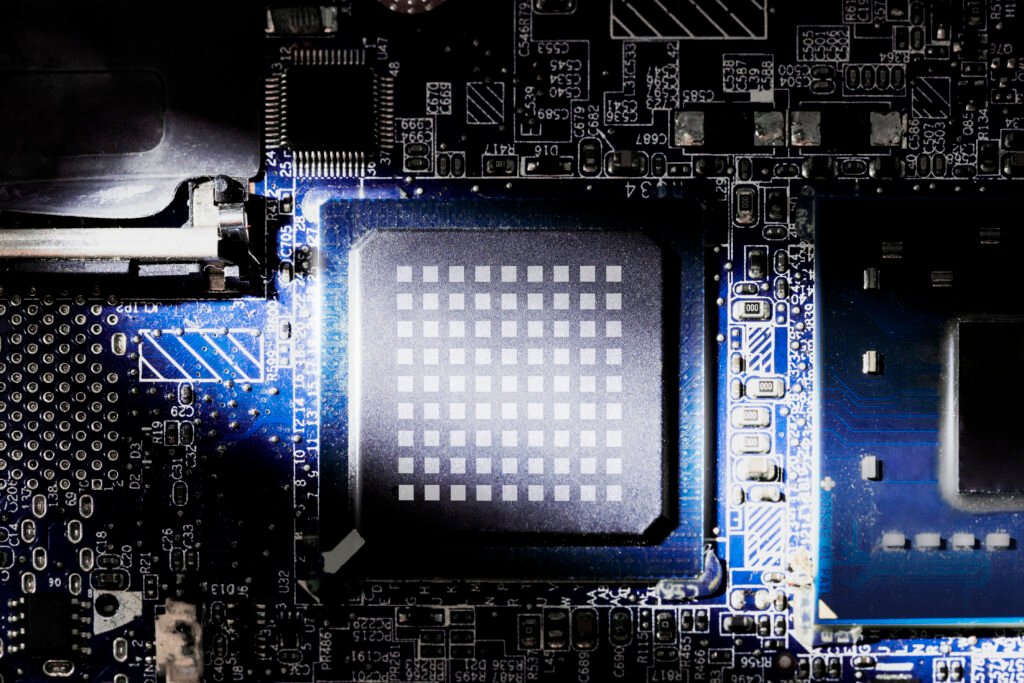
From the moment an aircraft takes flight to the intricate processes involved in satellite deployment and rocket propulsion, every component and system must undergo rigorous scrutiny to ensure optimal performance and safety.
In this blog, we delve into the critical role that tests and measurements play in the aerospace sector, elucidating their significance in guaranteeing the precision and reliability that define modern aviation and space exploration.
Importance of Precision and Reliability in Aerospace
In the dynamic realm of aerospace, precision, and reliability are not merely desirable attributes but fundamental prerequisites. The aerospace industry operates within a stringent framework where the slightest deviation from exactitude can have profound repercussions, ranging from compromised safety to substantial financial losses.
A. Safety Concerns:
Safety is paramount in aerospace, where even minor errors can lead to catastrophic consequences. Precision ensures that aircraft, spacecraft, and related systems function as intended, minimizing the risk of accidents and ensuring the well-being of passengers, crew, and assets.
Reliability, on the other hand, guarantees that these systems consistently perform within established parameters, reducing the likelihood of unexpected failures.
B. Impact on Performance:
Precision and reliability directly impact the performance of aerospace vehicles and equipment. In aircraft, precise aerodynamic designs enable optimal fuel efficiency, maneuverability, and speed, while reliable propulsion systems ensure consistent power output throughout flights.
Similarly, in space missions, precise trajectory calculations and reliable propulsion systems are imperative for achieving mission objectives and navigating the complexities of space.
C. Cost Implications:
The aerospace industry operates on tight margins, with substantial investments required for research, development, manufacturing, and operation. Precision and reliability directly influence the cost-effectiveness of aerospace endeavors. Errors or failures during testing or operation can lead to costly delays, rework, or even project cancellations.
Conversely, investments in precision engineering and rigorous testing can yield long-term savings by reducing maintenance costs, extending equipment lifespan, and mitigating risks associated with failures.
Overview of Test & Measurement in Aerospace Industry
In the aerospace industry, where cutting-edge technology meets the demands of extreme environments and high-performance requirements, the role of testing and measurement is central to ensuring the integrity and functionality of every component, from the smallest sensor to the largest propulsion system.
A. Definition and Scope
Test and measurement in aerospace encompass a wide array of techniques and methodologies aimed at assessing the performance, reliability, and safety of aerospace systems. This includes everything from assessing the structural integrity of aircraft frames to measuring the efficiency of propulsion systems and analyzing the aerodynamic characteristics of flight surfaces.
The scope of test and measurement in aerospace extends across various stages of development, production, and operation. It begins with the testing of individual components and materials in the research and development phases, progresses to comprehensive system integration tests during manufacturing, and continues with ongoing monitoring and maintenance throughout the operational lifespan of aerospace vehicles.
B. Key Components and Equipment Used
The tools and equipment employed in aerospace testing and measurement are as diverse as the systems they evaluate. They range from traditional instruments like pressure gauges, thermocouples, and strain gauges to sophisticated sensors, data acquisition systems, and advanced imaging technologies such as infrared cameras and X-ray tomography.
Moreover, specialized test rigs and facilities are often utilized to simulate real-world operating conditions, allowing engineers to subject aerospace components to extreme temperatures, pressures, vibrations, and other environmental stressors. These facilities include wind tunnels, thermal chambers, and centrifuges, among others.
C. Types of Tests Conducted
Aerospace tests and measurements encompass a multitude of tests tailored to assess different aspects of aerospace systems. Some common types of tests include:
- Structural Testing: Evaluating the strength, stiffness, and fatigue life of structural components through techniques like static load testing, fatigue testing, and modal analysis.
- Environmental Testing: Subjecting aerospace components to simulated environmental conditions, including temperature extremes, humidity, vibration, and electromagnetic interference, to ensure they can withstand the rigors of operation.
- Performance Testing: Assessing the performance characteristics of propulsion systems, flight control systems, avionics, and other critical subsystems to verify compliance with design specifications and operational requirements.
- Non-Destructive Testing (NDT): Employing techniques such as ultrasound, X-ray, eddy current testing, and thermal imaging to detect defects, flaws, and irregularities in aerospace materials and components without causing damage.
- Flight Testing: Conducting actual flight trials to validate the performance, handling qualities, and aerodynamic behavior of aircraft and spacecraft in real-world conditions.
Ensuring Precision: Test & Measurement Techniques
In the aerospace industry, ensuring precision is not merely a desirable attribute but an absolute necessity. Test and measurement techniques form the cornerstone of this endeavor, providing engineers and manufacturers with the tools necessary to verify the accuracy and reliability of critical components and systems. Below, we explore some of the key techniques employed to ensure precision in aerospace applications:
A. Metrology and Calibration Processes:
Metrology, the science of measurement, plays a central role in aerospace manufacturing. Precise measurements are essential for components ranging from turbine blades to avionics systems.
Calibration processes are employed to maintain the accuracy of measurement instruments over time. This involves comparing the performance of a device against a known standard and making adjustments as necessary.
Advanced metrology techniques, such as laser interferometry and coordinate measuring machines (CMMs), enable engineers to achieve micron-level accuracy in component dimensions.
B. Non-Destructive Testing (NDT) Methods:
NDT methods allow engineers to inspect materials and structures without causing damage, making them invaluable in aerospace applications where integrity is paramount.
Techniques such as ultrasonic testing, eddy current testing, and radiographic testing are used to detect defects such as cracks, voids, and delaminations in materials.
NDT methods are employed throughout the lifecycle of aerospace components, from initial manufacturing to in-service inspection and maintenance.
C. Computational Fluid Dynamics (CFD) Simulations:
Aerodynamics plays a critical role in the performance of aircraft and spacecraft. CFD simulations enable engineers to predict the behavior of fluid flow around complex geometries.
By solving the Navier-Stokes equations numerically, CFD simulations provide insights into factors such as lift, drag, and thermal management, allowing designers to optimize aerodynamic performance and fuel efficiency.
CFD simulations are used extensively in the design and testing of aircraft wings, engine nacelles, and spacecraft re-entry vehicles, helping to ensure optimal performance and safety.
Ensuring Reliability: Quality Assurance and Testing
In the aerospace industry, ensuring the reliability of components and systems is of utmost importance to guarantee the safety of passengers, crew, and assets. This reliability is achieved through meticulous quality assurance processes and rigorous testing protocols.
A. Material Testing:
Materials used in aerospace applications must withstand extreme conditions including temperature variations, pressure differentials, and mechanical stresses. Material testing involves subjecting samples to various stressors to assess their mechanical properties, durability, and resistance to corrosion and fatigue.
Advanced techniques such as non-destructive testing (NDT) methods like ultrasound, X-ray, and eddy current testing are employed to detect flaws or defects that could compromise the integrity of components.
B. Structural Testing:
Structural testing evaluates the performance and integrity of aerospace structures under simulated operational conditions. This includes static testing to assess structural strength and stiffness, fatigue testing to determine the durability of materials over time, and dynamic testing to evaluate responses to vibration and shock.
Test specimens are subjected to loads that mimic those experienced during flight or space missions, allowing engineers to validate designs and identify potential weaknesses before they become critical issues.
C. Environmental Testing:
Aerospace systems must withstand a wide range of environmental conditions, from the vacuum of space to the intense heat of re-entry into Earth’s atmosphere. Environmental testing simulates these conditions to evaluate the performance and reliability of components and systems.
Tests may include thermal cycling to assess thermal expansion and contraction, vibration testing to simulate the effects of launch and operation, and altitude testing to replicate the low-pressure conditions encountered at high altitudes. These tests ensure that aerospace systems can operate safely and reliably in the harsh environments they will encounter during their lifespan.
By subjecting components and systems to rigorous quality assurance and testing procedures, aerospace engineers can identify potential issues early in the development process, mitigate risks, and ultimately ensure the reliability and safety of aerospace vehicles and equipment. These efforts contribute to the overall success of missions and advancements in aviation and space exploration.
Challenges and Innovations in Test & Measurement
In the ever-evolving landscape of aerospace technology, test and measurement methodologies face a myriad of challenges, alongside continuous innovation aimed at overcoming these obstacles and enhancing efficiency, accuracy, and reliability.
A. Integration of New Technologies
The integration of cutting-edge technologies such as the Internet of Things (IoT), Artificial Intelligence (AI), and automation has revolutionized test and measurement processes in the aerospace industry. IoT-enabled sensors gather real-time data from aircraft components, allowing for predictive maintenance and early detection of potential failures.
AI algorithms analyze vast amounts of data to identify patterns and anomalies, improving the accuracy of test results and reducing human error. Automation streamlines testing procedures, increasing throughput and minimizing downtime.
B. Addressing Complex System Interactions
Aerospace systems are highly complex, comprising numerous interconnected components that must function harmoniously for optimal performance. Testing these systems involves simulating a wide range of operating conditions and evaluating their interactions under various scenarios.
Challenges arise in accurately replicating real-world conditions in controlled test environments and comprehensively assessing the performance of interconnected systems. Innovations in multi-disciplinary simulation tools and advanced modeling techniques help engineers simulate complex system interactions with greater fidelity, enabling more accurate predictions of performance and behavior.
C. Regulatory Compliance and Standards
The aerospace industry is subject to stringent regulatory standards and certification requirements aimed at ensuring the safety and airworthiness of aircraft and spacecraft. Compliance with these standards necessitates meticulous testing and validation of every aspect of aerospace systems, from materials and components to entire aircraft structures.
However, keeping pace with evolving regulations and standards poses a significant challenge for aerospace manufacturers and testing laboratories. Innovations in test and measurement technologies, coupled with collaborative efforts between industry stakeholders and regulatory bodies, are essential for achieving compliance efficiently while maintaining high standards of safety and reliability.
D. Environmental Considerations
Aerospace systems operate in a wide range of environmental conditions, including extreme temperatures, pressures, and vibrations. Testing these systems under realistic environmental conditions is crucial for assessing their performance and reliability. However, replicating such conditions in controlled test environments presents significant challenges, particularly when testing large-scale aerospace structures or systems. Innovations in environmental testing facilities and techniques, such as multi-axis vibration tables and thermal chambers, enable engineers to subject aerospace components and systems to a wide range of environmental conditions accurately.
Conclusion
In the dynamic and demanding field of aerospace engineering, where precision and reliability are paramount, the role of test and measurement stands as a cornerstone of innovation and progress. Throughout this exploration, we have witnessed the critical importance of rigorous testing in ensuring the safety, performance, and airworthiness of aircraft, spacecraft, and related systems.
Despite the myriad challenges that confront the aerospace industry in the realm of test and measurement, from the complexities of system interactions to the ever-evolving landscape of regulatory compliance, advancements in technology and methodology continue to drive progress forward. Through the integration of cutting-edge technologies like IoT, AI, and automation, alongside the refinement of environmental testing capabilities and the relentless pursuit of regulatory compliance, aerospace engineers and researchers are equipped with the tools and insights necessary to navigate the challenges of tomorrow.
As we look to the future of aerospace engineering, one thing remains clear: the relentless pursuit of precision and reliability through rigorous testing and measurement will continue to underpin the advancements that propel humanity further into the skies and beyond. By embracing innovation, collaboration, and a steadfast commitment to excellence, the aerospace industry is poised to soar to new heights, ushering in an era of unparalleled achievement and exploration.